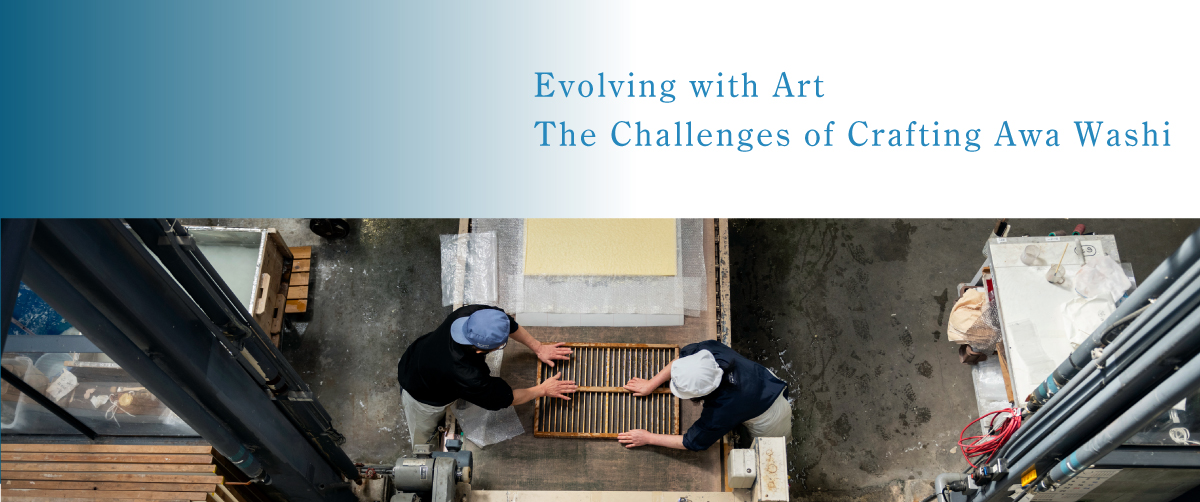
Washi, or Japanese paper, is a traditional craft that enriches our lives and one in which Japan takes great pride. While demand for washi products has fallen as life in Japan has Westernized, these products are still highly valued around the world for their durability and beautiful textures, and people are once again appreciating washi for its cultural value, as well. Awagami Factory in Tokushima Prefecture produces a brand of washi that preserves the traditions of Awa Washi, a specialty of the region, while also innovating with unique products that meet the needs of today. Awagami Factory has discovered new demand from a variety of sources, and communicates the appeal of Awa Washi, attracting attention from countries around the world. At the heart of this approach is the desire to carry the strong local washi culture into the future.
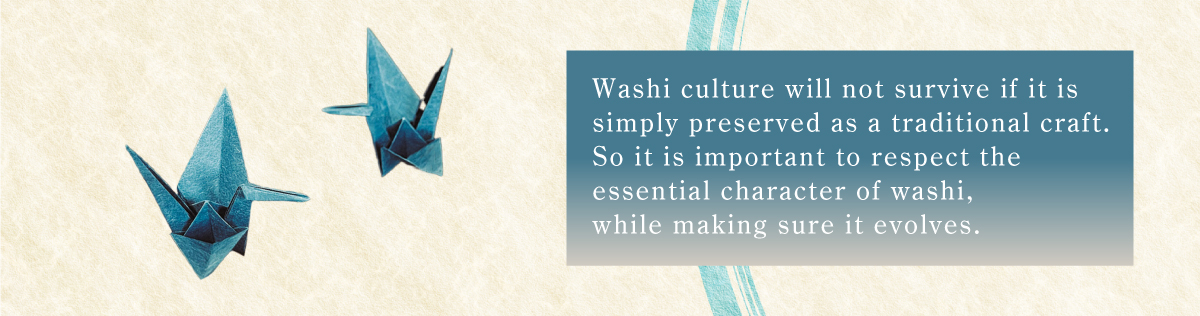
Flowing west to east through Tokushima, the Yoshino River crosses the Shikoku mountains from its source in central Shikoku. Along with the Tone River and Chikugo River, the Yoshino River is one of Japan’s three mightiest rivers, boasting a great abundance of water. As such, the water transportation industry developed here, primarily to ship supplies to the Kansai region, and various manufacturing techniques were refined in areas along the river.
“Kozo (paper mulberry) and mitsumata (Oriental paper bush) used to grow in the area of the Shikoku mountains, and the gampi shrub also grows well in the soil of the Asan mountain range. The land here is blessed with the plants, and the clean Yoshino River water was ideal for making washi, so in this sense it was only natural that it came to be a papermaking region.” So says Shigeyuki Nakajima, representative of the Fuji Paper Mills Cooperative Association, the parent company of Awagami Factory.
“There is a mountain called Mt. Koutsusan, which is a well-known symbol of the community here in Yamakawa-cho. Its other name is Mt. Yuuma. The fact that yuu refers to kaji (Broussonetia papyrifera), which was often identified as kozo paper mulberry, is another indication that washi papermaking is an industry with a long history in this region.”Awa Washi is made in Yamakawa-cho in Yoshinogawa City, located along the middle reaches of the Yoshino River. The historical town dates back some 1,300 years. This was when the Inbe clan, which served the imperial court of Japan, entered the country of Awa, and the Awa-Inbe group of Inbe craftsmen began to cultivate hemp and kozo. The fact that this is mentioned in the Kogo Shui, the historical record of the Inbe clan compiled in 807, suggests that washi production had already begun by the Nara period (710–794).
Made using the traditional washi techniques of nagashisuki (papermaking in flowing water) and tamesuki (papermaking in stored water), Awa Washi is a popular paper well known across Japan for its strength and water resistance, as well as for its simple texture and supple softness. At the height of the Meiji era (1868–1912), there were over 500 Awa Washi manufacturers along the Yoshino River. However, after World War II as demand for traditional paper gradually declined with the Westernization of life in Japan, many washi manufacturers went out of business. The Fujimori family, the sole remaining washi-making family, founded the Fuji Paper Mills Cooperative Association, which joined forces with the Awa Handmade Washi Commercial and Industrial Association, a group of handmade washi craftspeople, and the Hall of Awa Japanese Handmade Paper, a facility that aims to educate and pass on Awa Washi traditions. Together, the three entities developed the Awagami Factory brand of Awa Washi.
Nakajima explains, “In order to keep the traditions of Awa Washi alive, we have continued to produce washi that meets the needs of our customers. We’ve said yes to requests that seemed impossible and developed the new techniques we needed through a process of trial and error. There are still dozens of washi producers in other areas, like Echizen and Mino, that divide their businesses into two, making washi for shoji sliding doors as Company A and washi for calligraphy paper as Company B, but we are the only group that produces Awa Washi. Which is why, in order to survive, we had to take in a wide range of requests to produce washi for any application.”
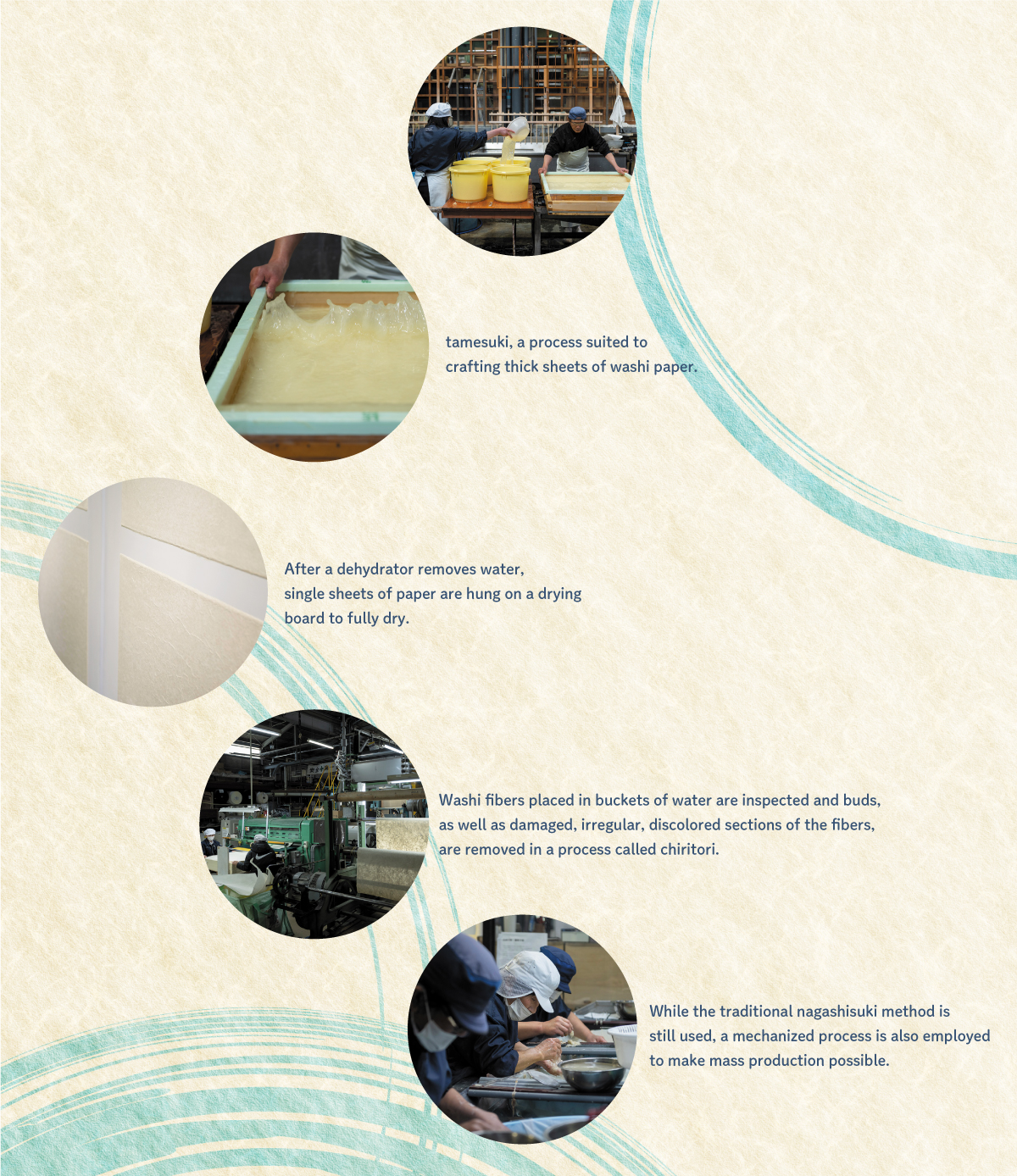
Today, Awagami Factory produces and sells a wide variety of products that highlight the texture and design of washi paper. One of these is Aizome Washi, washi paper dyed with indigo, another traditional Tokushima Prefecture industry. The indigo produced in Tokushima Prefecture is called Awa Ai and is shipped across Japan, gaining such renown that it is said “when you think of indigo, you think of Awa.” Yamakawa-cho in Yoshinogawa City, where Awagami Factory is located, is home to many indigo growers, and Awa Washi dyed with Awa indigo had been produced in the past. With the widespread use of chemical dyes, however, the Aizome Washi traditions had long died out. But then Minoru Fujimori, the previous Awagami Factory paper master, and his wife, Tsune, made the decision to revive Aizome Washi. After learning the indigo-dyeing technique from the ground up, the two set out to improve the papermaking and dyeing methods. The result is Awa Washi with a beautifully nuanced blue coloration.
“No matter how long and strong the washi fibers, they will dissolve and fall apart when soaked in an alkaline dye. So they applied konjac paste to both sides of the washi paper to make it water resistant,” says Nakajima.
Washi is submerged in a solution made from sukumo (fresh Awa indigo leaves that are dried and fermented) and has a brown look at the moment it emerges. Once rinsed and exposed to air, however, the paper oxidizes and quickly develops an indigo color. Color gradations are achieved by adjusting the length and frequency of dyeing, and the patterns created by layering colors combine with the textural quality of the Awa Washi for a beauty of great depth.
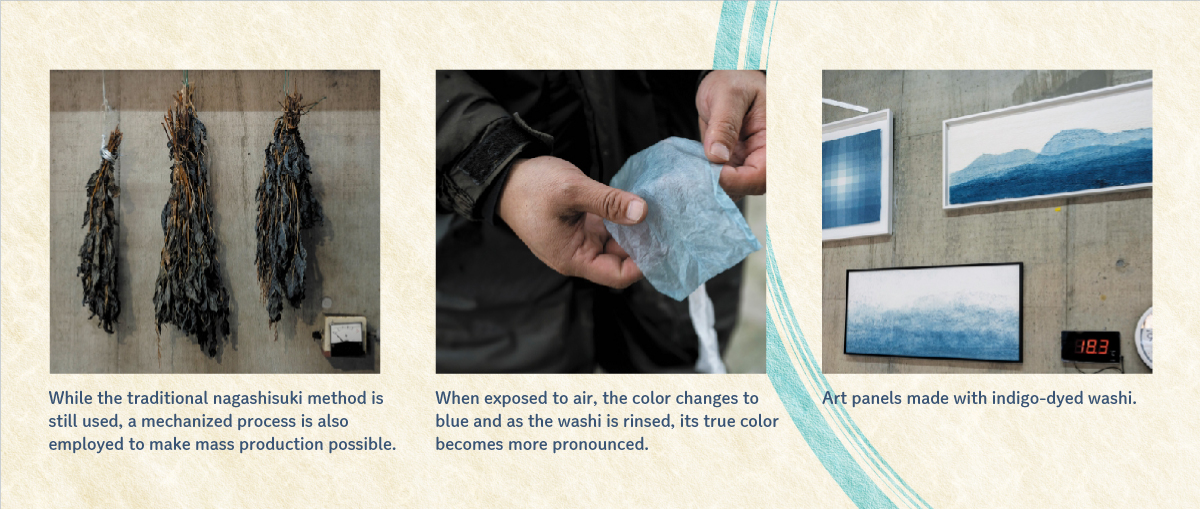
Creating new demand for Awagami Factory paper was crucial if the area was to continue as a washi production center. To develop new sales channels, they turned their attention to overseas markets.
“Washi has always been popular overseas as high-quality paper and has been exported to many countries since the Taisho era (1912–1926). But Japanese paper goes through a number of distributors before it reaches foreign retailers, so customers do not know the paper’s origin or producer. This is why we decided to launch the Awagami Factory brand and expand sales channels on our own. To do that, we have focused on educating people on the appeal of handmade washi. I have travelled overseas to teach people how to make washi, but now we welcome people who want to learn about washi at the factory and hold week-long workshops every year to teach the entire process for handmade washi. About 70 to 80% of the participants come from outside Japan, including museum curators who use washi for restorations and teachers who teach printmaking at art school. As a result overseas distribution has gradually increased. Now we have customers in 60 countries,” explains Nakajima.
Making connections with artists working within and outside of Japan was another important aspect of establishing Awa Washi as a brand. Through overseas workshops and ongoing educational activities, Awagami Factory has connected with painters, sculptors artists, photographers, printmakers and other artists. With an increasing number of requests from these artists for original washi products, Awagami works with them to develop new papermaking techniques to craft the washi suitable for the pieces they wish to create.
“There is a strong preference outside of Japan for thicker washi, and we have also received requests for large sheets of washi over five meters long. At some point, while we were working to fill these requests, Awa Washi came to be known as a brand that can provide large, thick sheets of washi for artwork,” explains Nakajima.
Awagami Factory not only provides technical guidance and assistance on how to create pieces, but also offers a fully equipped workshop for artists to use to create artwork. Awagami has set up a lab furnished with a papermaking area, a printmaking studio, and a large-scale inkjet printer to support creative activities
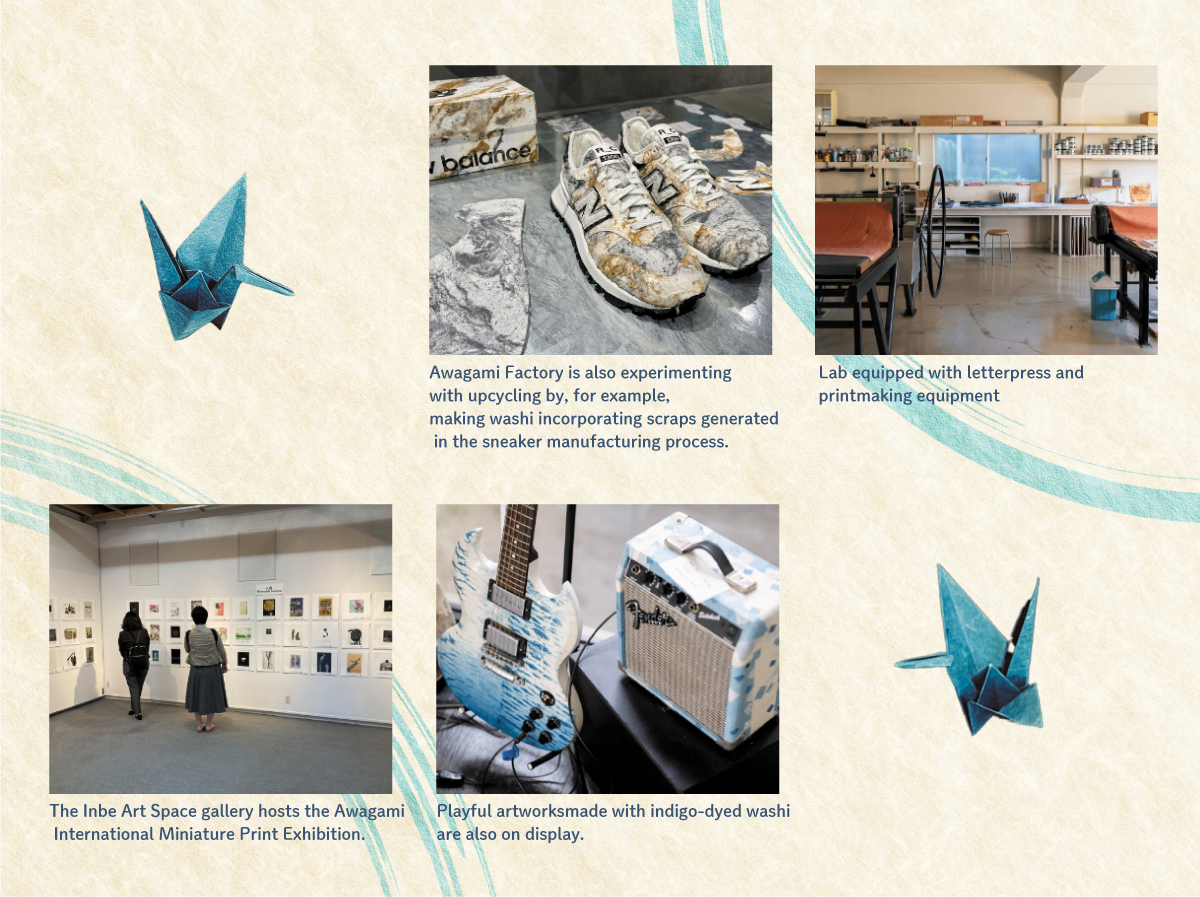
“In addition, the Awagami International Miniature Print Exhibition is held every two years to encourage the internationalization of handmade washi and to provide an opportunity for artists to showcase their work. Only artwork that uses washi paper is eligible for the competition. The sixth exhibition, held last year, attracted 1,052 applicants from countries all over the world, with a total of 1,587 submissions,” says Nakajima with a smile.
Awagami Factory also incorporates new technologies to produce unique washi paper and products that meet today’s needs, such as washi for inkjet printing, interior décor washi like wallpaper and art panels, and premium design lifestyle goods. As Nakajima points out, “Traditional crafts will not survive if they are simply preserved as is.” Awagami Factory continues to develop new washi that blends tradition and innovation, introducing even more washi possibilities to the world.
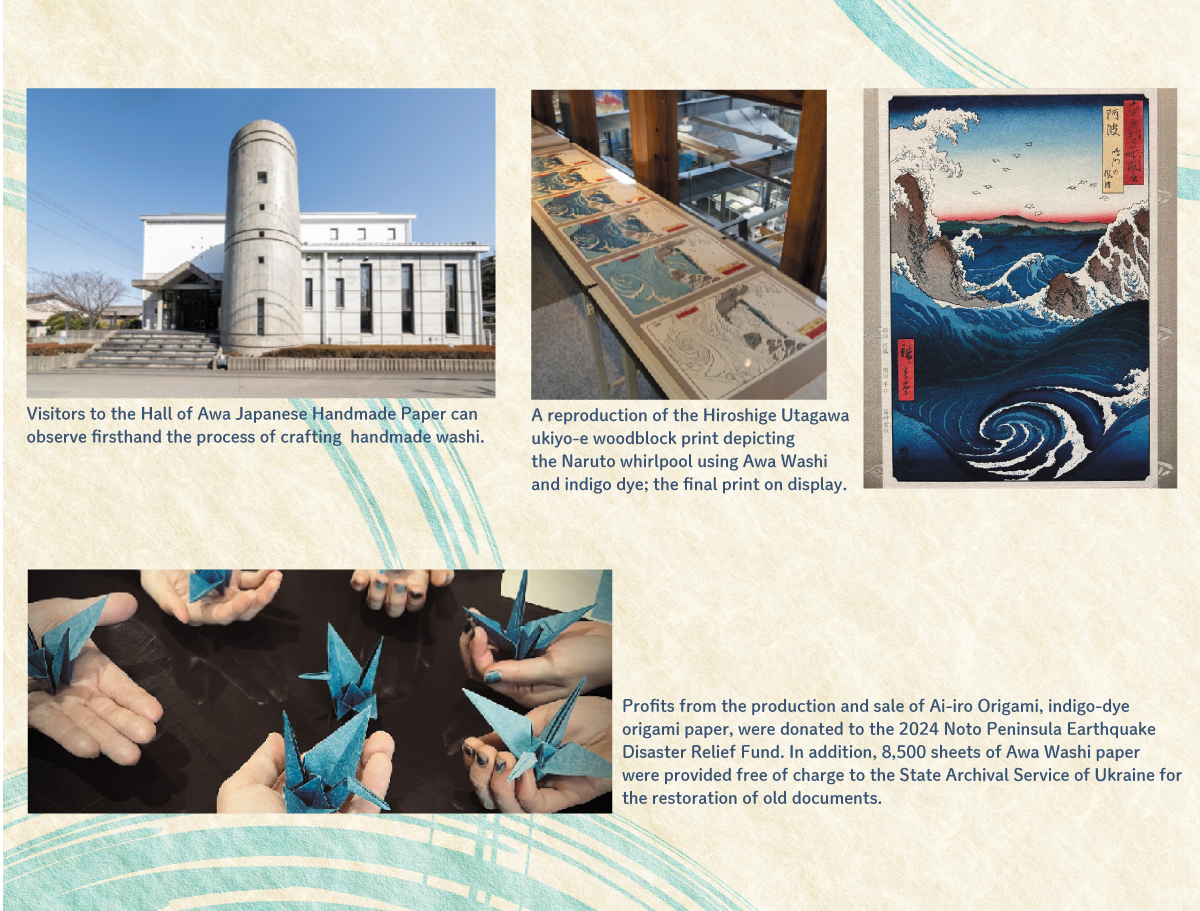
Shigeyuki Nakajima
Representative of the Fuji Paper Associatio
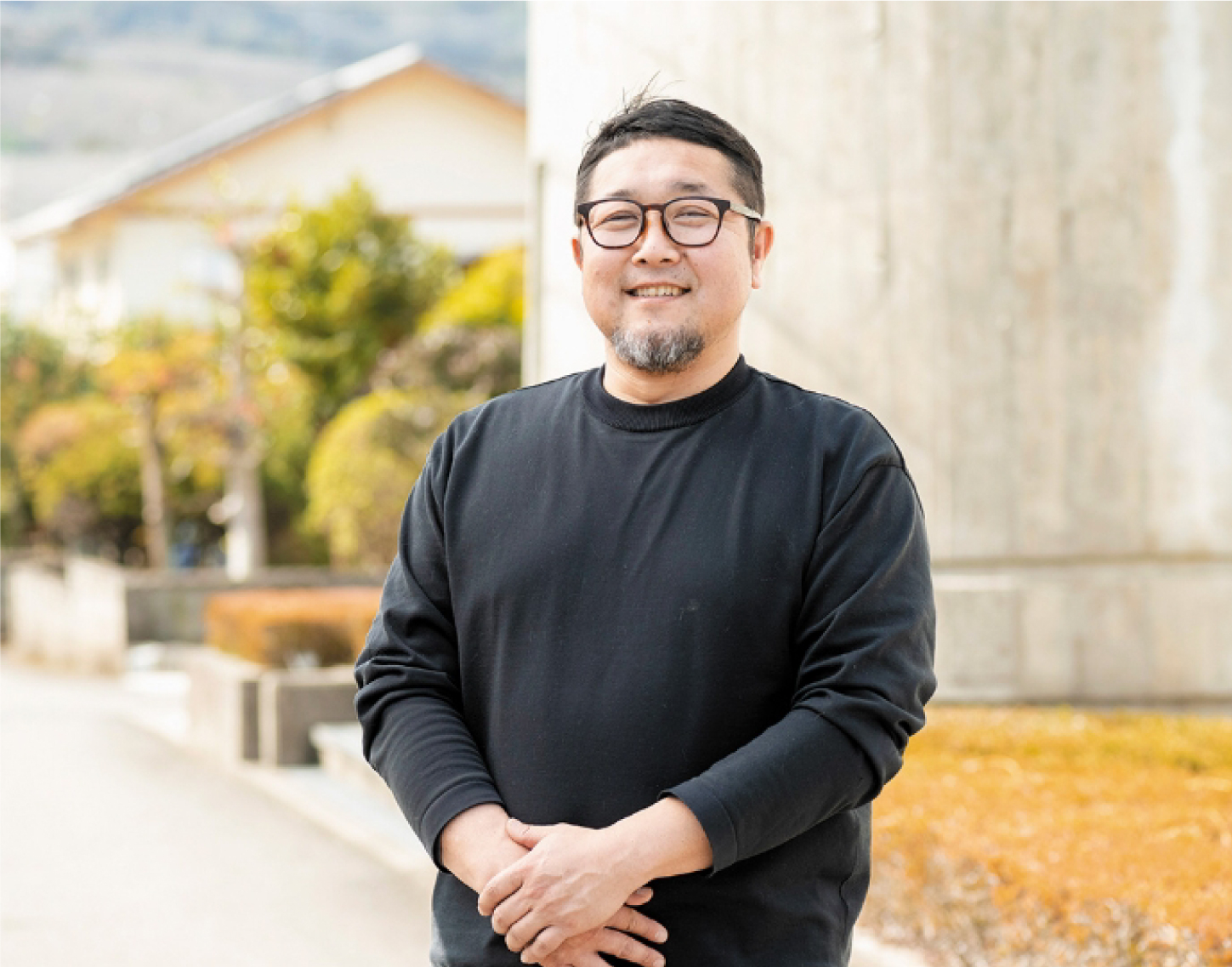
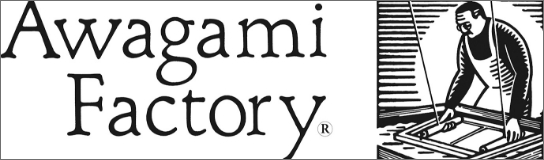
Awagami Factory Address: 141 Kawahigashi, Yamakawa-cho, Yoshinogawa City, Tokushima PrefectureTel: +81-883-42-2772 Official website: https://awagami.com/ |