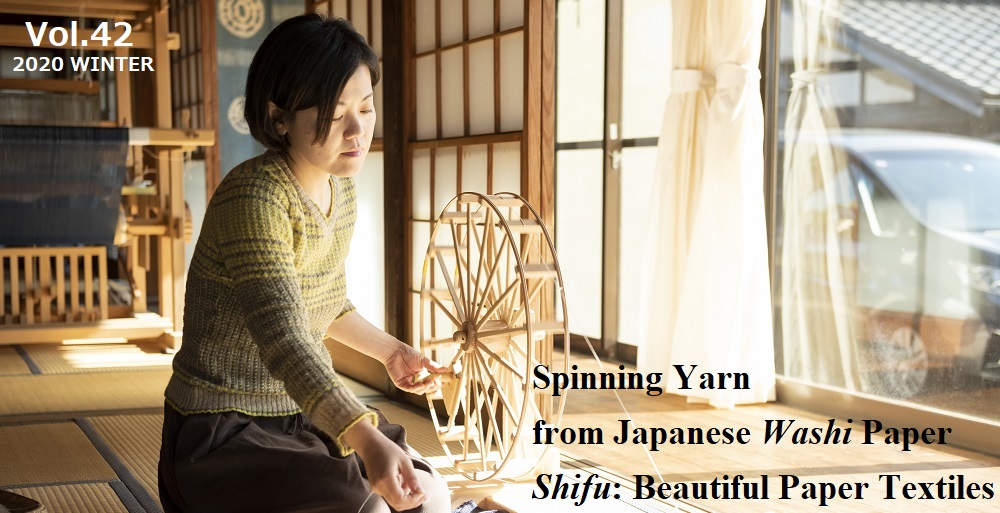
━━━━━━━━━━━━━━━━━━━━━━━━━━━━━━━━━━━━━━━━━━━━━━━━━━━━━━━━━━━━━━━━━━━━━━━━━
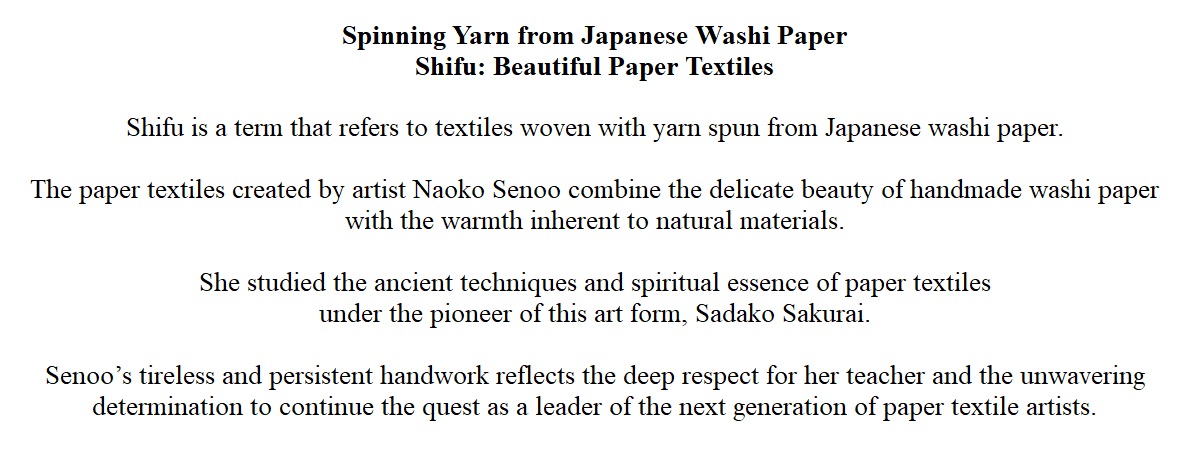
━━━━━━━━━━━━━━━━━━━━━━━━━━━━━━━━━━━━━━━━━━━━━━━━━━━━━━━━━━━━━━━━━━━━━━━━━
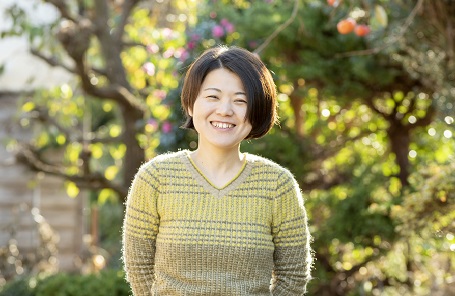

Born in Kyoto City, Kyoto Prefecture. Graduated from the Kyoto University of Art and Design. In her student days, Senoo developed a fascination with the world of Japanese washi paper, and after graduation she pursued the craft of handmade Japanese washi paper at an Echizen paper atelier in Fukui Prefecture. Later, Senoo relocated to Okinawa to study textile dyeing and weaving. Driven by a desire to deepen her knowledge in both Japanese paper and textiles, she took up an apprenticeship with Sadako Sakurai, moved to Ibaraki Prefecture, and is now engaged in paper textile creation.
Shifu literally means a cloth (fu) made from paper (shi). Japanese washi paper is cut into very fine strips, which are then spun into yarn and woven into a fabric. Paper textile manufacturing was conducted as a supplementary business at washi production regions throughout Japan, but starting in the Meiji period (1868-1912), it declined due to the spread of natural materials such as cotton, silk, and wool, and synthetic fibers such as polyester and nylon.
Today, paper textiles are manufactured on a small scale in a limited number of regions only.
“Until the mid-Edo period (around 1700-1750), cotton was an expensive fabric for ordinary people, so they used mainly hemp for their everyday attire. Clothes made from hemp, however, were stiff and provided poor protection against the cold, so people learned to use washi paper as an easily available alternative to hemp. They finely cut old and no-longer-needed accountant books and other materials made from washi, and spun the strips into yarn. Some preserved clothing items from that period feature patterns that are actually traces of the ink used for writing on the paper,”
explains Naoko Senoo, a paper textile artist. She says she learned everything there is to know about paper textiles as an apprentice to Sadako Sakurai, the still-active pioneer of the paper textile art in Japan, before relocating to Hitachi-Omiya City in Ibaraki Prefecture, which is famous as a Nishinouchi washi paper producing region. There, she established an atelier in a traditional Japanese house open to natural light and wind, and has since been creating paper textiles that reflects her unique sensitivity.
1. Fold
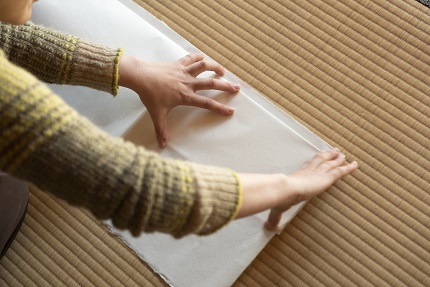
Arrange sheets of high-quality 100% kozo (mulberry) paper with strong well-intertwined fibers into a set of four, and fold them in byobu-datami (accordion fold), leaving a 1 – 1.5cm-wide flap in the upper part.
4. Knead
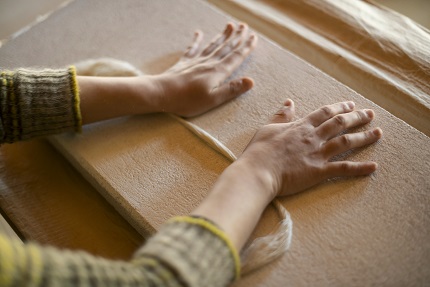
Place the moistened paper on a flat stone and knead with quick movements. As a result, the 2mm-wide strips take the form of round strings, like yarn.
2. Cut
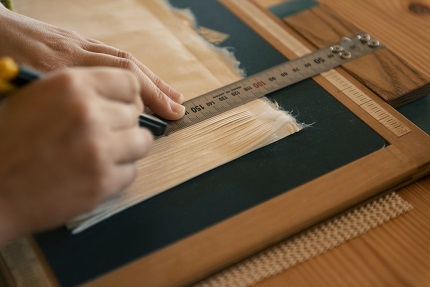
Use a special ruler to cut the Japanese washi paper (60x90cm) into 2mm-wide strips, without making cuts in the flap portion.
5. Spin
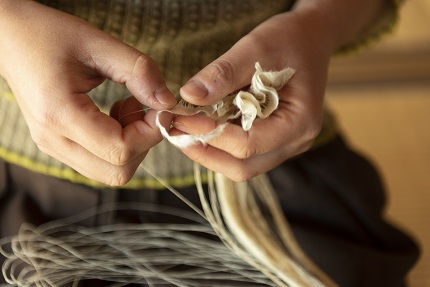
Remove the flap portion by hand, and manually twist the joints to form a single long and thin paper yarn thread.
3. Moisten
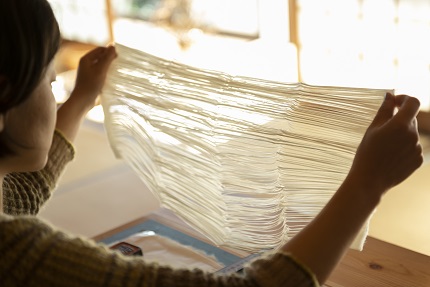
Place the cut paper between wet towels and leave to moisten for 6-7 hours. Adjust the moisture levels by spraying as necessary, depending on the weather and the humidity.
6. Twist
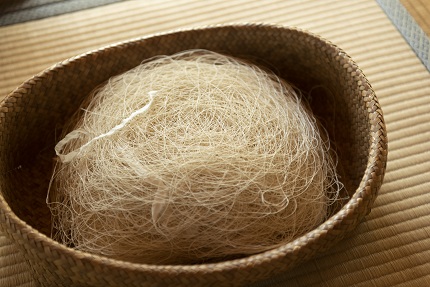
Place the paper thread on a spinning wheel and twist it, then twine it around a boiled bamboo stick. Apply plant dye to the paper yarn as necessary, and then weave it using a loom to complete the fabric.
Senoo’s paper textile works, displayed in the hall of her house, fascinate with an appearance and texture so elaborate and beautiful that it is hard to believe they are made of paper. At the same time, however, her textiles boast the warmth, quality, and elegant luster inherent to washi paper, and they feel pleasantly soft and smooth to the touch.
“Presently, I receive many requests to create kimono obi belts. Such belts made from paper fabrics are highly valued because of the paper’s properties to absorb humidity from the body, which helps the belt preserve its shape and yet feel light and unconstricting. In addition to obi belts, I receive many orders from frequent kimono wearers for white decorative collars that are sewn onto the robes worn under the kimono. I also make shirts and other Western-style garments using paper textiles. I create not only original paper fabrics in which both the warp and the weft are made of paper yarn, but also textiles in which the weft is made of paper but the warp is made of silk, hemp, or cotton. In principle, I select the yarn for the warp depending on the way of use and purpose of the garment,” explains Senoo.
She performs all operations by hand—from the selection of the washi paper most appropriate for the piece of clothing to be created, through the yarn spinning and plant dyeing, to the loom weaving—so it takes her between two and three months to complete a single piece in which both the warp and the weft are made of paper.
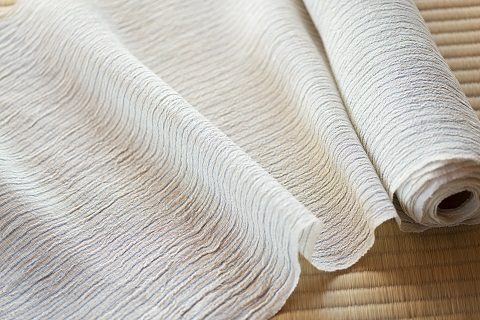
A stretch fabric made using silk yarn as warp and paper yarn as weft. The texture feels pleasant to the touch, with smoothness unique to paper textiles.
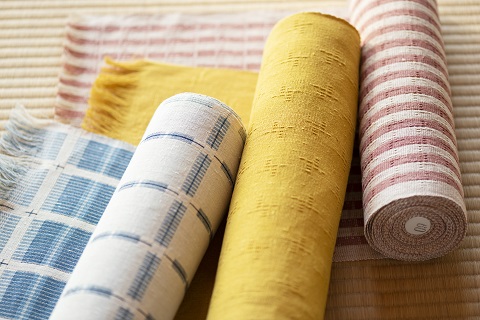
Paper textile obi belts made using paper yarn as both warp and weft. The red one is dyed with akane pigment, the yellow one with enju pigment, and the blue one with indigo pigment.
For Senoo, who studied oil painting at the Kyoto University of Art and Design, the practical courses in making canvasses and wood engraving, which were implemented as part of the study curriculum, triggered an interest in the tools and materials used in handcrafts born from Japan’s specific natural features. After graduating university, she traveled to various washi producing regions, and took a job at an atelier that specialized in Echizen paper, one of Japan’s best-known types of washi paper. After studying the craft of handmade paper for approximately four years, Senoo relocated to Okinawa, where she spent six and a half years learning traditional Shuri-ori textile weaving techniques.
“In the Okinawan atelier, I was given the opportunity to perform all operations myself: from obtaining raw silk from silkworms to dyeing the threads. I frantically studied everything that I wanted to know, and just when I was beginning to consider the future directions of my work, I happened to come across a magazine article about Sadako Sakurai’s paper textiles, and was stunned by their beauty.”
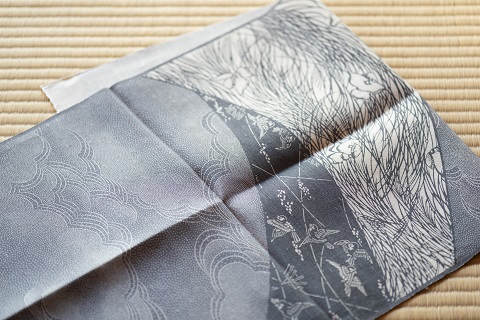
Works made from silk and paper textiles with patterns created by Hiromi Kikuchi, a master of Edo komon (tiny and intricate design dyed using pattern papers).
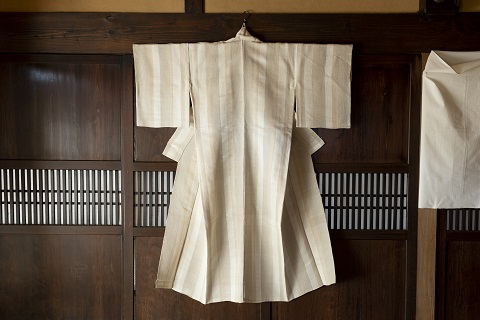
Kimono (temporarily tacked) created by Naoko Senoo based on techniques restored by Sadako Sakurai.
Sadako Sakurai is a venerable authority in the field of paper textiles. She spent years researching production techniques using the few remaining literary sources in order to restore the craft of paper textiles as it was born in Shiraishi of the old Sendai Domain (present-day Shiraishi City, Miyagi Prefecture). Today, in her 90s, she is still actively engaged in creative activities. Fascinated by her works, Senoo immediately contacted her via an acquaintance, and relocated to Ibaraki Prefecture, where Sakurai lived. Initially, Sakurai declined to take her as an apprentice, claiming she could not bear such a responsibility, but eventually Senoo’s persistence paid off and she was given the opportunity to study from scratch the art of paper textiles.
“It took Ms. Sakurai several decades to arrive at the answers that I learned from her in a mere 2 to 3 years. For this reason, I believe that, in my creative work, I must sufficiently understand and perfectly digest all I have learned. I want to study more, while re-examining and sorting the knowledge acquired so far, including the characteristics and possibilities of various plants, and the research of fiber materials,” says Naoko Senoo.
Just like her respected teacher, Senoo constantly keeps challenging herself to try new things. Her latest challenge is a collaboration with a stencil dyeing artisan to create artworks that feature Ise katagami (paper stencils for dyeing textiles) designs applied onto white paper fabrics. This bold attempt to re-invent paper textiles as an artform tailored to modern lifestyles and based on superb traditions will most certainly blaze new trails in the development of paper textiles.
━━━━━━━━━━━━━━━━━━━━━━━━━━━━━━━━━━━━━━━━━━━━━━━━━━━━━━━━━━━━━━━━━━━━━━━━━