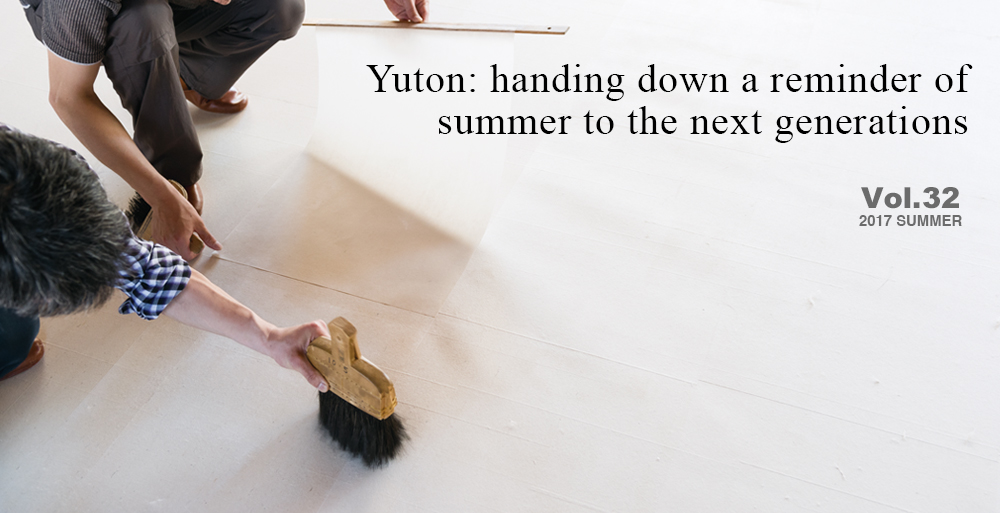
The yuton is a Japanese traditional mat consisting of layers of washi (Japanese paper) onto which oil is applied.
When it comes into contact with your skin, the smooth surface of the yuton absorbs the heat from your body and helps you stand the heat of summer.
The yuton is extremely durable, and has been used in many parts of Japan since the ancient past. In fact, it is proclaimed as a commodity that can withstand a century of use.
Beniya Koyodo, a hyogu(paperer) shop located in Sabae-shi, Fukui, is the only remaining manufacturer of yuton today.
The Japanese climate and the predecessors’ wisdom developed and passed the yuton down through generations.
The yuton also conveys the exquisite techniques and sense of mission of the stubbornly uncompromising craftsmen, and the spiritual richness that many Japanese people are leaving behind.
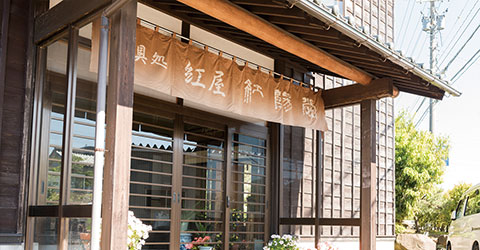
Beniya Koyodo
■Address: 2-10 Tamura-cho, Sabae-shi, Fukui
■Phone: 0778-62-1126
■Fax: 0778-62-2870
Beniya Koyodo undertakes the mounting of art works on materials such as hanging scrolls, byobu, frames, fusuma and shoji, and also restores old paintings and calligraphic works. The technique for manufacturing yuton is designated by Fukui prefecture as an intangible cultural property.
Uchiwa and Sensu (types of Japanese traditional fans) provide a gentle breeze. Furin (wind bells) bring coolness by their tinkling sound. Sudare and Yoshizu (types of reed screens) block sunlight and the public eye, and bring a cool airflow into the room. All these commodities were invented to help people to spend the hot, humid summers in Japan as comfortably as possible. Their predecessors secured a means of helping people get through the hot summers by exercising ingenuity in their everyday lives and going to the effort of obtaining materials from nature.
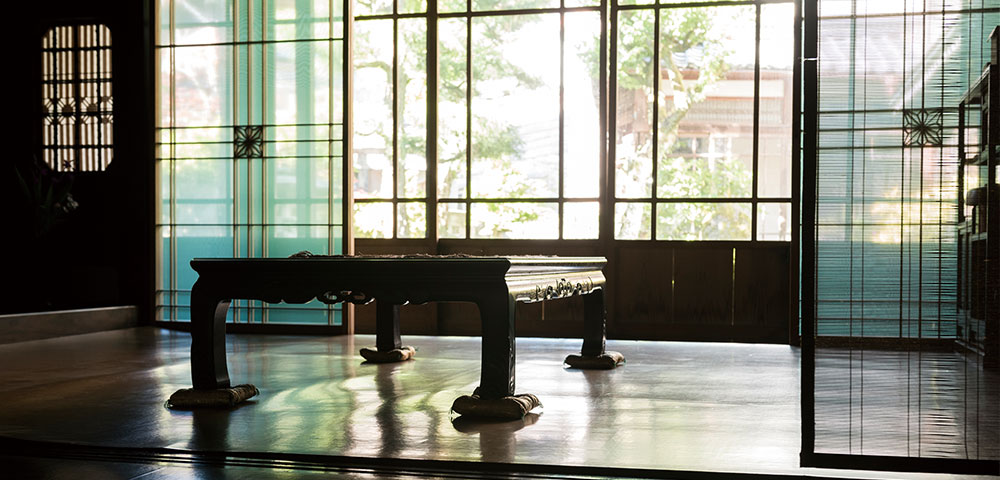
Yuton are made by applying perilla oil to the surface of layers of washi(Japanese paper). They are laid on tatami mats. Like mats made from rushes and cane, yuton are made from plant-derived material. Because of their cool tactile feel, yuton have long been appreciated as a summer necessity. However, yuton were used more frequently by temples, high-class restaurants and prestigious families than by general households due to their high price: the manufacture of yuton requires the use of a large quantity of high-quality washi, as well as a great deal of time and effort. Today, yuton are manufactured in only one place in Japan. Beniya Koyodo, a hyogu(paperer) shop located in Sabae-shi, Fukui.
“Just explaining it would not convey what it is like, and you won’t understand unless you try it. First of all, lie down on it,” Mr. Tomomi MAKINO, the third owner of Beniya Koyodo, says with a smile. “The yuton is a summer mat. You take it out of the closet in June and put it away again before October. Many people do it when they update their wardrobe for the change of seasons.” He invited us to his home and kindly suggested that we sit on the yuton.
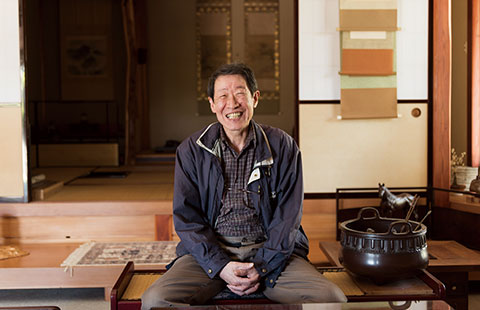
Mr. Tomomi Makino, the third owner of Beniya Koyodo.
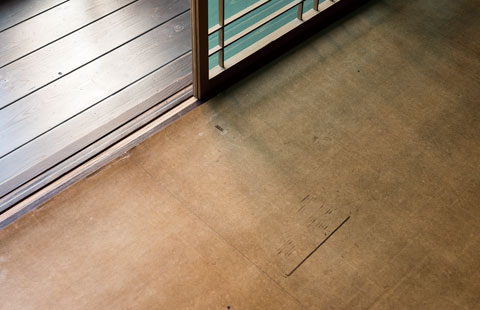
The yuton that is in Mr. Makino’s home.
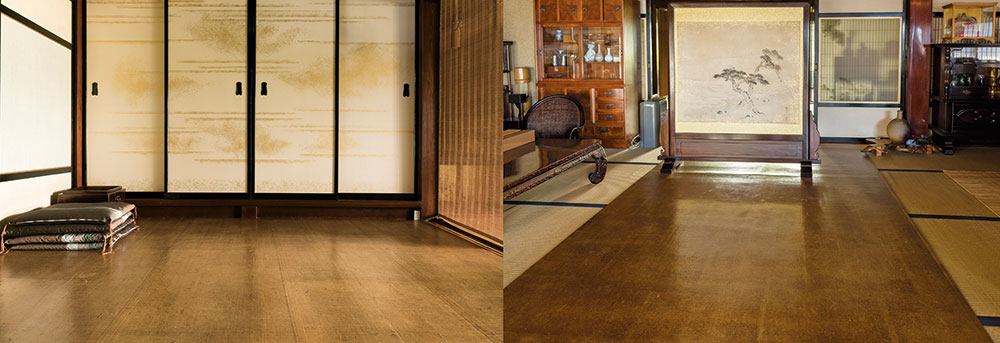
The more you use it, the darker its caramel color becomes and the more character it has.
The surface of the yuton is lustrous like a mirror, with a deep caramel color. It is so lustrous that pillars, shoji screens and even the table legs are reflected in it. I lay down on it and touched it. It was certainly cool and comfortable, visually conveyed an impression of transparency and also felt cool both tactually and visually. “My children always lie down on it in summer, and look very comfortable,” Mr. Makino’s words eloquently describe its comfort.
Why do yuton feel cool? We asked him to explain the mechanism of their coolness. “When we appeared on a TV program, they performed a scientific verification, but the mechanism of the coolness was not elucidated,” says Mr. Makino. “One scientist said that the oil on the surface, which easily conveys heat, might let the heat out, and that the layer of washi that contains air might absorb the heat. They attempted to verify this hypothesis with the use of thermography, but the thermal conductivity was not very good. Another hypothesis says that the effects of the vaporization of heat might cool it. This has not been demonstrated either.” Even today’s science cannot elucidate the predecessors’ wisdom.
We were also allowed to enter the atelier where yuton are manufactured. The sound of washi being pounded with the hake (brush) could be heard throughout the boarded spacious atelier. The process of making yuton starts from piecing together the stout washi called torinokoshi on a yutondai, a large piece of washi. The torinokoshi is trimmed to the finished size and wheat gluten glue is applied to it before echizen washi, Japanese paper made solely from the paper mulberry, is pasted to it. A hard keba made from hemp palm is used to pound the washi and the paper fibers are pulled up, which combines the fibers of the washi and strengthens their adhesion. The pounding with the hake is repeated until the 14 layers of washi are thinned to 2 – 3 millimeters. The washi is pounded about ten thousand times for eight tatami mats. The craftsmen do this in a crouching position throughout the process. It is a physically strenuous job. The washi is then left for a while to dry before persimmon tannin is applied to the back and perilla oil is applied to the front. It is sun-dried and polished with tofu crushed in a cotton cloth, and is then finished. Making one sheet of yuton takes nearly one month with the combined efforts of three workers. Since the process is very labor and time intensive, yuton are expensive, costing nearly 140,000 yen per tatami. A yuton will last for more than 100 years. The more you use it, the better it works. It is worth the price.
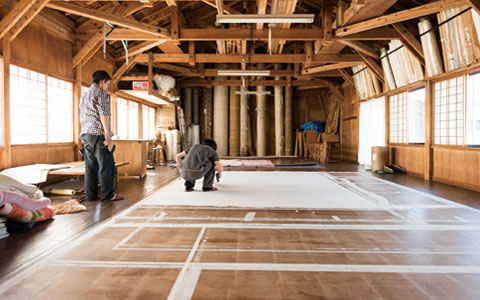
The spacious atelier is dedicated to yuton making.
The work of pasting washi must continue ceaselessly in order to prevent the glue from drying.
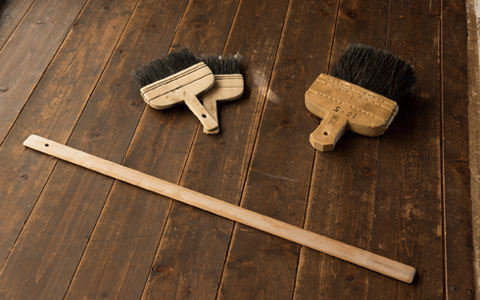
Uchibake (right) is designed to mix the fibers of the top and bottom washi, whereas nadebake (left) is used to apply wheat gluten glue to the washi.
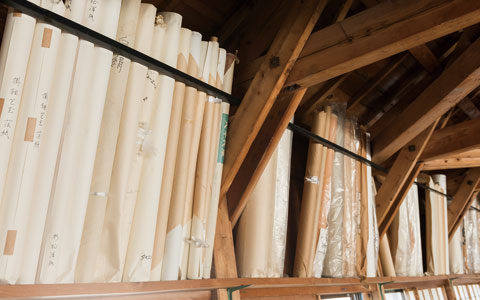
Mr. Makino collected the high-quality handmade washi from around the country.
In recent years, he has not used any paper other than echizen washi, which is manufactured in his hometown, to make yuton.
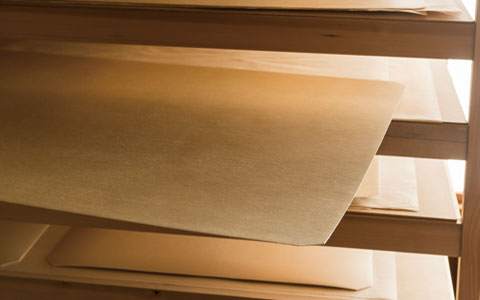
Brand-new yuton.
Beniya Koyodo is a well-established hyogu shop that will celebrate its centennial anniversary this year. It undertakes the mounting of art works on materials such as hanging scrolls, frames and byobu and makes, repairs and repapers building materials such as fusuma and shoji. Today, houses have become westernized and tokonoma (alcoves) and Japanese-style rooms continue to decrease. Beniya Koyodo consistently receives requests for specific types of mounting that no other shop can do, and for the restoration of valuable cultural properties. “We call our business hyogu. In kanji, the word hyogu means ‘furnishing the surface.’ ‘Surface’ here refers to the calligraphy or drawing art. If someone sees a work of art and likes its hyogu, it means we did a poor job because the hyogu is not intended to outshine the art on it. Our job is highly appreciated and successful if the person likes the picture that is on the hyogu,” said Mr. Makino. His words convey his pride as a craftsman who understands and fulfills the essence of his job.
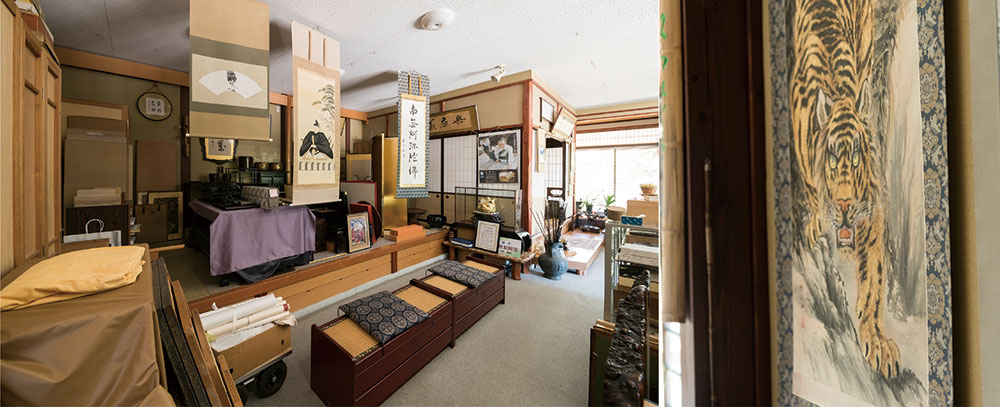
Beniya Koyodo undertakes the decoration of temple walls and kinbyobu (gilt folding screens) as well as general hyogu materials such as byobu (folding screens), shoji, fusuma (types of paper sliding door) and hanging scrolls. They are also knowledgeable in the restoration of works of art. They were involved with numerous works that are kept in museums around the world.
He also says that the practice of making yuton can only be performed by a specialist who is thoroughly aware of the characteristics of washi, cloth, glue and the other materials and has delicate skills and abundant know-how. “Beniya Koyodo has made yuton since my grandfather established the company. To make better products, my grandfather visited other hyogu shops and paid to observe and learn each step. I heard that is how he acquired the technique,” said Mr. Makino.
“We are not the only reason that yuton making has survived in Fukui. Another reason is the climate of monozukuri(Japanese manufacturing style), which is unique to this place.” Tannan, located in central Fukui, is a rare area in the world where traditional industries are concentrated. Tannan has a 90% share of domestic eyeglass manufacturing. In addition, washi, lacquerware, forged blades and many other items are manufactured here. The traditional culture of monozukuri has taken root in Tannan. This is an important factor that has helped pass down the yuton-making technique.
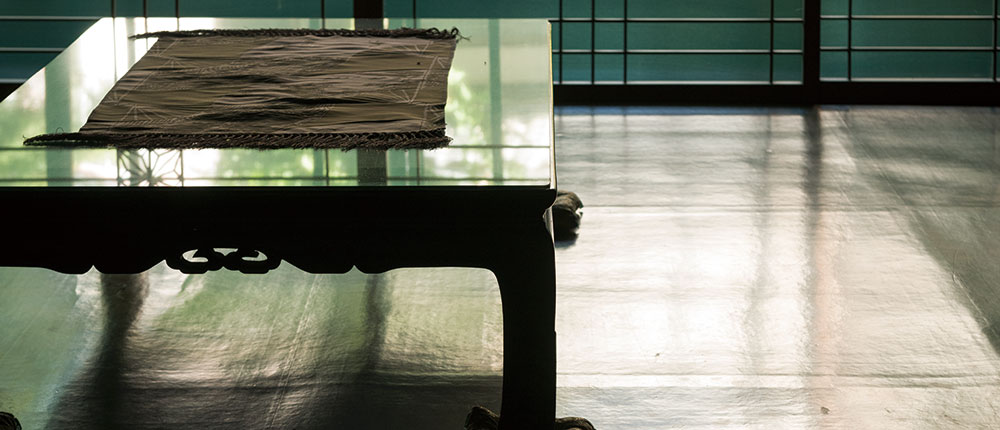
Literature on yuton is limited, but yuton are said to have already existed in the Edo period. Mr. Makino says. “The origin of yuton is probably ondol (a kind of underfloor heating that was popular on the Korean Peninsula. A thick sheet of paper impregnated with oil was pasted on the floor to make it easier to feel the warmth of the floor). Ondol did not become popular in Japan, where the climate is not as cold as on the Korean Peninsula. But it is considered that Korean people applied the technique of ondol to the origination of yuton in Japan. So it is ridiculous to argue that we monopolize a method that was taught by others. So, I tell anyone who wants to know, including my apprentices, how to make yuton.”
Lastly, we asked him the reason for continuing yuton making despite the fact that it takes a lot of trouble and effort. His answer was simple: “Because we believe that a yuton is a good thing to have.” “We cannot live the way we do today without the wisdom of our predecessors. Because this is really a good product packed with tireless effort and wisdom, we will keep making it as long as we can,” said Mr. Makino.
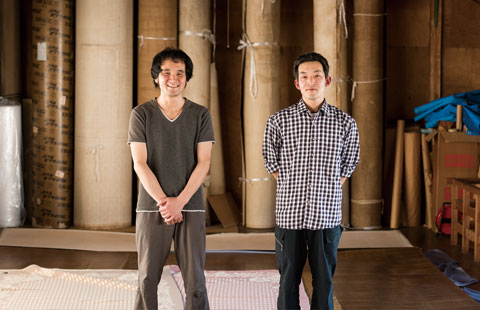
Mr. Yoshinao Makino (left) strives to improve his skills and studies under his father, who is the third owner of the shop. The other man is his apprentice Mr. Hikaru KIMURA.
The technique of yuton making was inherited by Mr. Makino from his father and grandfather and is being handed down to his son, Mr. Yoshinao MAKINO. His son’s ambition is “none other than carefully making yuton for our customers. Whether the yuton lasts for 100 years depends on our handwork.” This comment fully conveys the young craftsman’s authentic wish to uncompromisingly keep making good products.
“Coexist with nature.” Unfortunately, we are gradually leaving behind the wisdom and knowledge that was accumulated by our predecessors. The evolution of technology has certainly brought us many benefits. On the other hand, it is also true that technology cannot give us every kind of richness. The yuton may provide us with a clue to a better future.